+91 9881153232 / +91 9552666833

MechTech Inframine
Stationary Crushers and Sand Washing Plants
We want all of our customers to experience the impressive level of professionalism when working with Trinity Enterprises. All of our services, especially this one, exist to make your life easier and stress free. You can trust us to supply you with the best products, as well as top quality customer service.

Stone Crushing and Sand Washing Plants Range
Where ENGINEERING Surpasses Trades
Mechtech Engineers was incorporated by a group of qualified and well trained engineers with a vast experience in the field of design, manufacturing, supply and commissioning of different types of crushing & screening equipment’s and plants.

Jaw Crusher
Jaw Crusher-Working of the top-of-the-line series
Mechtech’s top-of-the-line MTJ-type jaw crushers are designed specifically for primary applications where resizing is the primary goal. They allow the material to be handled within the confines of your crushing plant. The jaw crusher must have a good and homogeneous feed level to perform optimally.
These single-toggle jaw crushers have a deep, symmetrical crushing chamber, a large feed opening for their size, and an ideal nip angle that provides smooth material flow and high reduction efficiency. Jaw crushers typically have a reduction ratio of 1:2 or 1:3. This ratio is influenced by the bulk density, crushability, size distribution, and moisture content of the feed material,among other factors, and will affect the performance of the crushing chamber.
Compressive and rubbing pressures are used in a single-toggle grease lubricated jaw crusher to break material. The two jaw plates of the crusher, one of which is immovable and the other movable, work together to exert this mechanical pressure. The crushing chamber is a V-shaped cavity formed by these two vertical manganese jaw plates, with the top of the chamber being larger than the bottom. Jaw crushers are sized by the crushing chamber’s top opening. A 41″ x 33″ jaw crusher, for instance, has two jaw dies that are 41″ wide and 33″ apart at the top opening, also known as the gape opening.
The discharge material is sized using the narrower opening at the bottom of the crushing chamber. A toggle plate and tension and pull-back rods keep the swing jaw tight near the bottom.
Since the crushing of the material is not performed in one stroke of the eccentric shaft, massively weighted flywheels are attached to the shaft and powered by a motor. The flywheels transfer the inertia required to crush the material until it passes the discharge opening. Generally, the motion of swing jaw is elliptical.

Cone Crusher
Mechtech Cone Crushers-MTC Series are of cutting-edge design, a small footprint, and high capacity relative to size.
Mechtech Cone Crushers-MTC Series are of cutting-edge design, a small footprint, and high capacity relative to size. Each model is adaptable, user-friendly, and extremely productive. This crusher is suitable for a wide range of tasks, including high-capacity secondary application and high-reduction tertiary or pebble-crushing application, at low operational and maintenance cost.
​
HIGH EFFICIENCY
This hydraulically adjusted cone crusher results in high efficiency and maximum output.
HIGH PERFORMANCE
It is robustly designed for optimum performance and ensures ease of transportation, installation, operation and maintenance.
HIGH QUALITY PRODUCTS
The proper combination of Concave and Mantle ensures high capacities and high output quality comparable to those of other brands.
LOW POWER USAGE
Least amount of power consumption per tone
of crushing.
WEAR RESISTANT
A well-sealed interior mechanism guarantees strong protection against dust and other foreign objects, thus reducing wear and tear.
LOW OPERATIONAL COST
The feed opening area and crushing chamber liner profile stay consistent throughout the wear life, thus decreasing the total operational costs.
EASE OF MAINTENANCE
The design of the Mech Tech Cone Crusher makes it incredibly simple to use and maintain. Since maintenance and inspection work is done from the top, it is easier to perform the job at low cost and with little downtime.
​
​
​
​
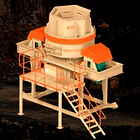
Vertical Shaft Impactor MTV Series
VSI
Mechtech Vertical Shaft Impactors(VSI) are engineered for higher capacity, low maintenance costs with least power consumption.
There is a huge demand for crushers that deliver perfect output while cutting cost in a sustainable way. Our VSI was engineered to meet such demand effortlessly.
​
ENERGY EFFICIENCY
Perfect feed material flow is controlled by the multi-flow hopper with multi-flow ports and Multi-flow Collection plates.
THREE-PORT ROTOR DESIGN
The most efficient and balanced solution is obtained by the three-port rotor design. The absence of the feed eye ring leads to less weight on the highest point of the rotor, thus reducing out of balance forces. The diameter and the height of the rotor provide efficient and low power consumption crushing.
AUTOGENOUS CRUSHER
Rock-on-rock collision means rock is crushed on rock and the materials are directly crushed thereby eliminating any wear parts.
LOW IMBALANCE FORCES
Out of balance forces are reduced by the optimized design and placement of upper and lower wear plates. It prevents unwanted streaming and provides a more stable rock bed and quick replacement through the inspection door. Absence of screws or nuts in aggressive areas leads to easy dismantling of wear parts.
​
​
​
​
​

Vibrating Screen
Mechtech inclined screens are versatile. They can be used for primary, secondary and tertiary screening. The standard slope angle of the screen is 18°, although it can be adjusted for specific applications. It is suitable for wet screening with spray pipes.
DURABLE BUILD
Inclined screens have a rugged design and circular motion to circulate material and avoid plugging, while also being designed with safety in mind to reduce operating hazards.
CUSTOMIZABLE
Inclined screens can be customized to improve operational efficiency and profitability, either as a stand-alone unit or as part of a multi- stage process.
HIGHER SCREENING EFFICIENCY
More output can be screened at a time as the screening area is more.
ENCLOSED DUST COVER(OPTIONAL)
Vibrating screens are also offered with 360° enclosed type dust cover to prevent air pollution.
INCREASED PRODUCTION
Because gravity forces material to move down the screen faster, inclined screens have a higher production capacity.
HIGH PERFORMANCE
It is robustly designed for optimum performance and ensures ease of transportation, installation, operation and maintenance.
LOW CAPITAL COST
Because inclined screens do not require as much power and are typically implemented with fewer shafts, they often require a lower capital investment.

Smooth Double Roll Crusher – SDRC Series
Mechtech SDRCs designed for primary, secondary and tertiary crushing are best suited for achieving the reduction ratios of 4:1. It is best suited for producing finer products. SDRCs are widely used and referred for their excellent reliability with simple designs and low maintenance.
ENERGY EFFICIENCY
Improve energy efficiency by up to 20 - 25%.
HIGH PRODUCTION EFFICIENCY
Higher Throughput
HIGHER PRESSURE MECHANICAL SYSTEM
Generates a high crushing force
DECREASED CIRCULATING LOAD
Lower Circulating load by up to 25 – 30 %
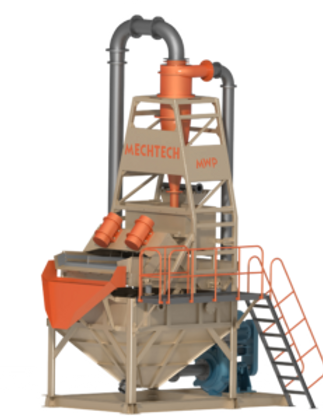
Sand Washing System
Mechtech Washing System cleans and separates materials to meet quality.
Mechtech Washing System cleans and separates materials to meet quality and specification requirements efficiently, ensuring that the final products are free from contaminants